Plastic extrusion services for specialized industrial applications
Plastic extrusion services for specialized industrial applications
Blog Article
Checking Out the Various Techniques and Technologies Behind Plastic Extrusion
The world of plastic extrusion is a blend of modern technology, precision, and innovation, crucial to numerous industries worldwide. Advanced machinery, electronic controls, and a selection of products converge in this complex process, producing premium, sturdy products.
Understanding the Basics of Plastic Extrusion
The procedure of plastic extrusion, commonly hailed as a keystone in the world of manufacturing, creates the bedrock of this discussion. Essentially, plastic extrusion is a high-volume production procedure in which raw plastic product is melted and formed into a continuous profile. It's a method widely employed for creating things with a continuous cross-sectional account, such as pipelines, window structures, and weather condition stripping. The process starts with feeding plastic materials, commonly in the kind of pellets, into a heated barrel. There, it is warmed and combined up until it comes to be molten. The molten plastic is after that required through a die, forming it right into the preferred form as it sets and cools down.
The Function of Different Materials in Plastic Extrusion
While plastic extrusion is a generally made use of strategy in manufacturing, the products made use of in this process significantly affect its final output. Different kinds of plastics, such as polyethylene, PVC, and Abdominal, each provide special residential properties to the end product. Manufacturers must very carefully consider the residential properties of the material to optimize the extrusion process.
Strategies Utilized in the Plastic Extrusion Process
The plastic extrusion procedure entails various techniques that are essential to its operation and efficiency (plastic extrusion). The conversation will start with a streamlined explanation of the fundamentals of plastic extrusion. This will be followed by a failure of the process in detail and an exploration of techniques to enhance the efficiency of the extrusion technique

Recognizing Plastic Extrusion Essentials
In the world of manufacturing, plastic extrusion stands as a basic procedure, essential in the manufacturing of a wide variety of daily items. At its core, plastic extrusion involves changing raw plastic product right into a constant profiled form. Essential understanding of these basics allows for more exploration of the more detailed elements of plastic extrusion.
In-depth Extrusion Refine Breakdown

Improving Extrusion Technique Effectiveness
Effectiveness gains in the plastic extrusion process can significantly affect both the high quality of the last item and the general performance of the procedure. Continual optimization of the extrusion strategy is vital to preserving a competitive side. Regular upkeep of extrusion devices can also reduce downtimes, thus raising productivity.
Just How Innovation Is Altering the Face of Plastic Extrusion
The introduction of new technology has significantly transformed the landscape of plastic extrusion. It has actually resulted in the advancement of sophisticated extrusion equipment, which has boosted the efficiency and quality of the plastic extrusion procedure. Innovations in the extrusion process have actually also been driven by technical improvements, supplying enhanced abilities and flexibility.
Advanced Extrusion Equipment
Transforming the world of plastic extrusion, advanced machinery imbued with advanced modern technology is ushering in a new age of performance and precision. These makers, outfitted with innovative functions like automatic temperature level control systems, guarantee optimal problems for plastic processing, therefore decreasing waste and improving product top quality. High-speed extruders, for example, intensify outcome rates, while twin-screw extruders offer exceptional mixing capacities, important for creating intricate plastic blends. In addition, electronic control systems use extraordinary accuracy in operations, minimizing human error. These makers are made for longevity, lowering downtime and maintenance expenses. While these developments are already remarkable, the continual development of innovation assures even greater jumps forward in the field of plastic extrusion equipment.
Innovations in Extrusion Procedures
Using the power of contemporary technology, plastic extrusion procedures are undergoing a transformative metamorphosis. Advancements such as electronic numerical control (CNC) systems now permit for more precision and uniformity in the production of extruded plastic. Automation even more boosts effectiveness, lowering human error and labor prices. The combination of artificial knowledge (AI) and machine learning (ML) algorithms is reinventing top quality control, forecasting inconsistencies, and boosting the total efficiency of check my source extrusion processes. With the arrival of 3D printing, the plastic extrusion landscape is also increasing into brand-new realms of opportunity. These technical innovations are not only improving the quality of extruded plastic items but also pushing the market towards a more sustainable, effective, and ingenious future.
Real-World Applications of Plastic Extrusion
Plastic extrusion, a reliable and functional procedure, locates use in plenty of real-world applications. The automotive market additionally utilizes this modern technology to create components like trim and plastic bed linen. The strength and adaptability of plastic extrusion, coupled with its cost-effectiveness, make it a crucial procedure throughout different industries, underlining its prevalent useful applications.
The Future of Plastic Extrusion: Predictions and Patterns
As we seek to the perspective, it comes to be clear that plastic extrusion is poised for considerable advancements and transformation. New technologies assure to reinvent the industry, from smart machinery that optimizes efficiency to lasting materials that lower environmental effect. Automation and robotics are forecasted to play a larger role, simplifying production and making certain constant quality. Green options to traditional plastic, such as bioplastics, are also expected to get grip. These materials not only assist to preserve resources yet additionally minimize waste, straightening with global sustainability goals. Innovations in 3D printing are predicted to open up new possibilities for personalization. These patterns suggest a vibrant, evolving future for plastic extrusion, driven by technological technology and a dedication to sustainability.
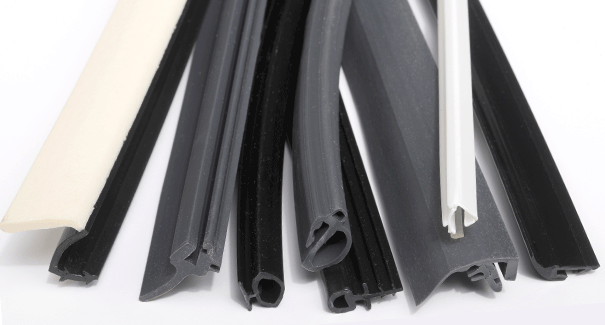
Conclusion
In verdict, plastic extrusion is an intricate procedure that utilizes sophisticated modern technology and varied products to create varied items. As plastic manufacturing continues to develop, it continues to be an important part of numerous markets worldwide.
In significance, plastic extrusion is a high-volume production process in which raw plastic material is melted and formed right into a constant profile.While plastic extrusion is a commonly used method in manufacturing, the materials utilized in this procedure greatly affect its final result. At its core, plastic weblink extrusion includes transforming raw plastic material into a continuous profiled shape. It has actually led to the advancement of advanced extrusion equipment, which has boosted the performance and high quality of the plastic extrusion process.In final thought, plastic click here to find out more extrusion is an intricate process that uses innovative modern technology and varied materials to produce varied items.
Report this page